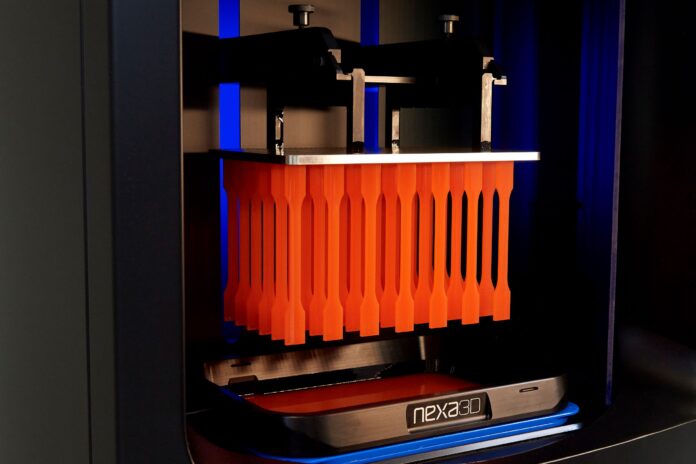
Το BMW Group εγκαινίασε επίσημα το νέο Κέντρο Προσθετικής Κατασκευής (Additive Manufacturing Campus) σε μια συντονισμένη προσπάθεια για την εξέλιξη της σχετικής τεχνολογίας. Επιταχύνεται, έτσι, η εξέλιξη των οχημάτων και η ενοποίηση της παραγωγής.
Το Κέντρο Προσθετικής Κατασκευής φιλοξενεί την παραγωγή πρωτοτύπων και εξαρτημάτων μαζικής παραγωγής κάτω από την ίδια στέγη, μαζί με την έρευνα για τεχνολογίες τρισδιάστατης εκτύπωσης και τη σχετική εκπαίδευση για εξάπλωση της παραγωγής χωρίς τη χρήση εργαλείων. Το campus αντιπροσωπεύει μία επένδυση ύψους 15 εκατ. ευρώ και θα αναδείξει το BMW Group σε πρωτοπόρο στη χρήση προθετικής κατασκευής στη βιομηχανία αυτοκινήτου.
Μιλώντας στην τελετή των εγκαινίων, ο Milan Nedeljković, Μέλος Δ.Σ. της BMW AG, υπεύθυνος Παραγωγής δήλωσε: “Η προσθετική κατασκευή είναι ήδη αναπόσπαστο κομμάτι του παγκόσμιου συστήματος παραγωγής μας σήμερα, και θεμελιώδες συστατικό της στρατηγικής μας για την ψηφιοποίηση. Στο μέλλον, νέες τεχνολογίες του είδους θα μειώσουν περαιτέρω τους χρόνους παραγωγής και θα μας επιτρέψουν να επωφεληθούμε ακόμα περισσότερο από τη δυνατότητα παραγωγής χωρίς τη χρήση εργαλείων”.
Από την πλευρά του, ο Daniel Schäfer, Ανώτερος Αντιπρόεδρος του τομέα Ενοποίησης Παραγωγής και Πιλοτικού Εργοστασίου στο BMW Group, σχολίασε: “Στόχος μας είναι η περαιτέρω εκβιομηχάνιση μεθόδων 3D εκτύπωσης στην παραγωγή αυτοκινήτων και η εφαρμογή νέων φιλοσοφιών αυτοματοποίησης στην αλυσίδα διαδικασιών. Με αυτό τον τρόπο θα μπορέσουμε να εκσυγχρονίσουμε τη κατασκευή εξαρτημάτων για μαζική παραγωγή και να επιταχύνουμε την εξέλιξη. Την ίδια στιγμή, συνεργαζόμαστε με τους υπεύθυνους εξέλιξης οχημάτων, παραγωγής εξαρτημάτων, αγορών και το δίκτυο προμηθευτών, καθώς και διάφορους άλλους τομείς της εταιρείας για τη συστηματική ενσωμάτωση και αποτελεσματική χρήση της τεχνολογίας”.
Η πολυετής εμπειρία και οι συνεργασίες προάγουν την τεχνολογία
Ο Jens Ertel, Διευθυντής του Κέντρου Προσθετικής Κατασκευής δήλωσε: “Τα τελευταία 30 χρόνια περίπου, το BMW Group έχει αναπτύξει ολοκληρωμένες δεξιότητες, που θα συνεχίσουμε να εξελίσσουμε στο νέο μας campus, το οποίο διαθέτει τα πιο σύγχρονα μηχανήματα και εφαρμόζει τις τελευταίες τεχνολογίες. Επιπλέον, οι μέθοδοι εξέλιξης και σχεδιασμού των εξαρτημάτων επιτρέπουν την ταχύτερη παραγωγή τους, συγκριτικά με τη χρήση συμβατικών μέσων, παρέχουν ευελιξία σχημάτων και τα καθιστούν πιο λειτουργικά”. Συνεχίζοντας, ο Ertel αναφέρθηκε στα εξής: “Εργαζόμαστε σκληρά ώστε να εξελίξουμε πλήρως την προσθετική κατασκευή και να επωφεληθούμε από αυτή όσο το δυνατόν περισσότερο σε όλο τον προϊοντικό κύκλο ζωής: από τη δημιουργία πρωτοτύπου μέχρι την παραγωγή, και από το στάδιο after-sales μέχρι τη χρήση σε κλασικά οχήματα”.
Πέρσι, το BMW Group κατασκεύασε περίπου 300.000 εξαρτήματα με τη μέθοδο της προσθετικής κατασκευής. Το Κέντρο Προσθετικής Κατασκευής απασχολεί αυτή τη στιγμή έως 80 εργαζόμενους και είναι εξοπλισμένο με 50 βιομηχανικά συστήματα επεξεργασίας μετάλλων και πλαστικών. Επιπλέον 50 συστήματα λειτουργούν σε μονάδες παραγωγής σε όλο τον κόσμο.
Η πρόσβαση στις τελευταίες τεχνολογίες επιτυγχάνεται μέσα από μακροχρόνιες συνεργασίες με κορυφαίους κατασκευαστές και πανεπιστήμια και με αναζήτηση νέων παικτών της βιομηχανίας. Το 2016, η BMW i Ventures – επενδυτικός βραχίονας του BMW Group – επένδυσε στην Carbon, μία εταιρεία με έδρα στη Silicon Valley, της οποίας η τεχνολογία DLS (Digital Light Synthesis) έφερε την επανάσταση στην παραγωγή ημιαγωγών μέσω επίπεδου προτζέκτορα φωτός για την επίτευξη ταχείας παραγωγής εξαρτημάτων.
Περαιτέρω επενδύσεις έγιναν το 2017, όταν το BMW Group συνεργάστηκε με την Desktop Metal, μία start-up που ειδικεύεται στην προσθετική κατασκευή μεταλλικών εξαρτημάτων και στην ανάπτυξη καινοτόμων, πολύ παραγωγικών διαδικασιών κατασκευής. Η συνεργασία με την Desktop Metal θα συνεχιστεί. Την ίδια χρονιά, η BMW i Ventures επένδυσε στην αμερικανική start-up Xometry, την παγκοσμίως κορυφαία πλατφόρμα για on-demand παραγωγή. Με ένα εκτεταμένο δίκτυο εταιρειών παραγωγής που ειδικεύονται σε τομείς όπως η τρισδιάστατη εκτύπωση, η Xometry παρέχει ταχεία πρόσβαση σε εξαρτήματα.
Η τελευταία επένδυση ήταν στη γερμανική ELISE, που επιτρέπει στους μηχανικούς να κατασκευάζουν το λεγόμενο ‘DNA εξαρτημάτων’ που περιέχει όλες τις τεχνικές προδιαγραφές, από απαιτήσεις φορτίων μέχρι περιορισμούς παραγωγής, κόστη και πιθανές παραμέτρους βελτιστοποίησης. Η ELISE χρησιμοποιεί στη συνέχεια αυτό το DNA, μαζί με εγκεκριμένα εργαλεία εξέλιξης, για αυτόματη παραγωγή βέλτιστων εξαρτημάτων.
Μέσα από τη συνεργασία με καινοτόμους εταίρους και πανεπιστήμια, το BMW Group προσπαθεί να επιταχύνει την εφαρμογή της προσθετικής παραγωγής και να δημιουργήσει το δικό του portfolio διαδικασιών.
Στάδια έρευνας και προ-εξέλιξης στην προσθετική κατασκευή
Η μονάδα (business unit) προ-εξέλιξης στο Κέντρο Προσθετικής Κατασκευής βελτιστοποιεί νέες τεχνολογίες και υλικά για ολοκληρωμένη χρήση σε όλη την εταιρεία. Η έμφαση εδώ δίδεται σε αλυσίδες αυτοματοποιημένων διαδικασιών που μέχρι πρότινος απαιτούσαν πολλή χειρωνακτική εργασία, ώστε η τρισδιάστατη εκτύπωση να γίνει πιο οικονομική και βιώσιμη για χρήση σε βιομηχανική κλίμακα μακροπρόθεσμα.
Σε ό,τι αφορά στην ανάπτυξη διαδικασιών 3D εκτύπωσης για χρήση σε βιομηχανική κλίμακα, τα ερευνητικά projects είναι ιδιαίτερα σημαντικά. Παράδειγμα τα προγράμματα Industrialisation (Εκβιομηχάνιση) και Digitisation (Ψηφιοποίηση) του Additive Manufacturing for Automotive Series Production (IDAM) project καθώς και το IDAM project, και τα δύο με την υποστήριξη του Γερμανικού Υπουργείου Παιδείας & Έρευνας. Με το IDAM, το BMW Group και οι 12 εταίροι του project προετοιμάζουν το δρόμο για την ενσωμάτωση της προσθετικής παραγωγής σε περιβάλλον μαζικής παραγωγής στη βιομηχανία αυτοκινήτου.
Στο Κέντρο Προσθετικής Κατασκευής, οργανώνεται μία γραμμή παραγωγής που αντιγράφει ολόκληρη την αλυσίδα διαδικασιών, από την προετοιμασία της ψηφιακής παραγωγής μέχρι την κατασκευή και αναθεώρηση των εξαρτημάτων. Η ομάδα του IDAM προετοιμάζεται τώρα για τις ειδικές απαιτήσεις της παραγωγής μεμονωμένων ανταλλακτικών. Οι στόχοι παραγωγής επιβεβαιώνουν την αξία αυτού του συνεργατικού εγχειρήματος ως ενός εμβληματικού project: η ετήσια παραγωγή αναμένεται να ανέλθει σε συνολικά τουλάχιστον 50.000 εξαρτήματα μαζικής παραγωγής, με πάνω από 10.000 μεμονωμένα εξαρτήματα και ανταλλακτικά, όλα θα κατασκευάζονται σύμφωνα με πολύ υψηλά πρότυπα ποιότητας και θα ενισχύουν το ρόλο του BMW Group ως πρωτοπόρου στην 3D εκτύπωση στη Γερμανία.
Το Κέντρο Προσθετικής Κατασκευής συνεισφέρει επίσης σημαντικά στη σειριακή παραγωγή πλαστικών εξαρτημάτων. Το POLYLINE project εστιάζει σε θέματα όπως η ψηφιακή διασύνδεση σταδίων διαδικασιών και η ανάπτυξη μιας μεθοδολογίας διασφάλισης σταθερής ποιότητας σε ολόκληρη την αλυσίδα διαδικασιών. Το Κέντρο Προσθετικής Κατασκευής θα ενορχηστρώσει επίσης τις προσπάθειες των 15 εταίρων της κοινοπραξίας του project με σκοπό τη δημιουργία και δοκιμή μιας αξιόπιστης, πλήρως διασυνδεδεμένης γραμμής παραγωγής για πλαστικά εξαρτήματα. Ευρήματα από το project αναμένεται να βοηθήσουν στη μείωση του κόστους παραγωγής σε ποσοστό 50%, με τεράστια συμβολή στη μαζική παραγωγή. Επιπλέον, ενιαίες μέθοδοι διασφάλισης ποιότητας θα αυξήσουν τη σταθερότητα των τεχνολογιών και θα καταστήσουν την παραγωγή πιο βιώσιμη.
Εκπαίδευση σε όλη την εταιρεία
Παράλληλα με την κατασκευή εξαρτημάτων, η ομάδα του Campus προσφέρει συμβουλευτικές υπηρεσίες και εκπαιδευτικά σεμινάρια σε εργαζόμενους της εταιρείας. “Για την επιτυχημένη εξάπλωση αυτών των τεχνολογιών, χρειαζόμαστε άριστα εκπαιδευμένους συναδέλφους σε όλο το δίκτυο, οι οποίοι έχουν καταλάβει πλήρως τα πλεονεκτήματα και τα χαρακτηριστικά τους. Για να μπορέσουν να τις αξιοποιήσουν, οι σχεδιαστές θα πρέπει να υιοθετήσουν μία νέα οπτική και μεθοδολογία στη φάση δημιουργίας των προσεχών εξαρτημάτων. Η τρισδιάστατη εκτύπωση επιτρέπει την παραγωγή σχεδόν οποιουδήποτε σχήματος, προετοιμάζοντας το δρόμο για νέα σχέδια και λειτουργίες. Στην εποχή μας υπάρχουν αμέτρητα εξαρτήματα που μπορούν να κατασκευάζονται μόνο μέσω της προσθετικής μεθόδου”, εξηγεί ο Jens Ertel.
Οι εγκαταστάσεις παραγωγής του BMW Group σε όλο τον κόσμο κατασκευάζουν ήδη εξαρτήματα μέσω 3D εκτύπωσης, τόσο για πρωτότυπα όσο και για οχήματα παραγωγής ή ως ειδικά εξαρτήματα για ορισμένους πελάτες. Η κατασκευή εξαρτημάτων εκεί όπου είναι απαραίτητα θεωρείται μία εύλογη λύση για το BMW Group, γι’ αυτό, οι διαδικασίες προσθετικής κατασκευής συμπληρώνουν άριστα τις υπάρχουσες τεχνολογίες παραγωγής.
Εφαρμογές στη Μαζική Παραγωγή
Το BMW Group ξεκίνησε για πρώτη φορά την προσθετική κατασκευή εξαρτημάτων το 1991, για πρωτότυπα οχήματα. Μέχρι το 2010, καθιερώθηκαν διαδικασίες βασισμένες σε πλαστικό και μέταλλο, αρχικά σε μικρότερες παρτίδες, για την παραγωγή μέσω τρισδιάστατης εκτύπωσης εξαρτημάτων όπως η φτερωτή της αντλίας νερού σε αγωνιστικά αυτοκίνητα του DTM. Περαιτέρω εφαρμογές μαζικής παραγωγής ακολούθησαν από το 2012 και μετά, με μία σειρά εξαρτημάτων για τα μοντέλα Rolls-Royce Phantom, BMW i8 Roadster (2017) και MINI John Cooper Works GP (2020), που περιλαμβάνει τέσσερα εξαρτήματα, προϊόντα 3D εκτύπωσης ως στάνταρ.